Through water conservation, pollution control, recycling, and water regime education, Bluestar has transformed its concept of water use, optimized its allocation, and made precise efforts to accelerate water ecological changes and build an efficient and water-saving enterprise.
Elkem: Innovating water ecological development models to make more responsible choices
As a silicon-based material manufacturer with business in the whole industrial value chain, Elkem takes practical actions to feed nature and express its attitude in its daily production and R&D.
Renewable hydropower
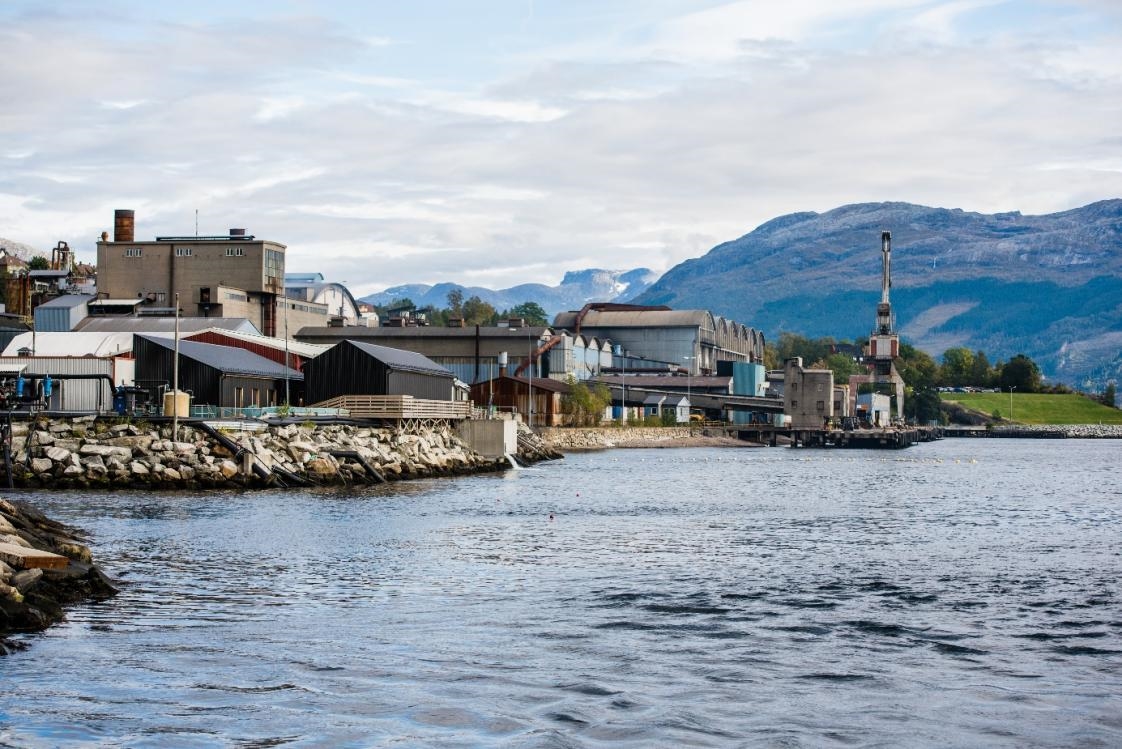
The plants in Bjølvefossen and Rana, Norway, realize clean production by developing and utilizing hydropower resources. Among them, the Rana plant generates about 30% of its electricity through renewable hydropower.
The Fiskaa plant in Norway and the Sarawak plant in Malaysia both carry out daily production based on renewable hydropower resources. Hydropower resources in Brazil’s two major production bases account for 91%.
Enabling the closed cooling water circulation system
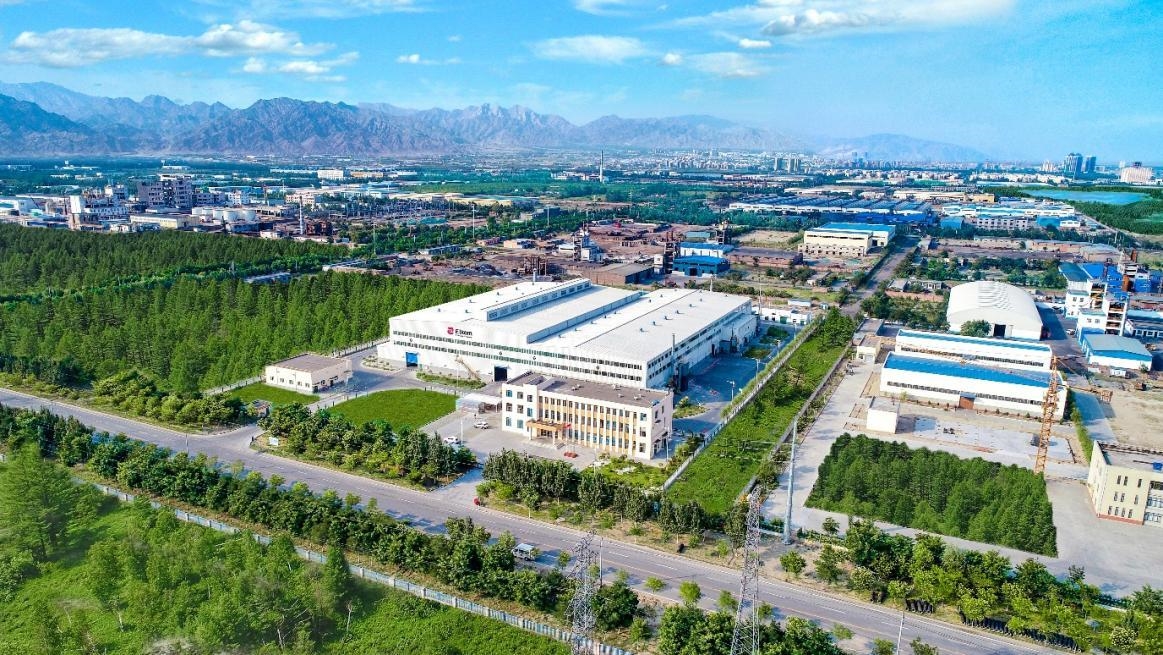
Committed to creating a circular economy model, Elkem Foundry China (EFC) has adopted a closed cooling water circulation process in its production process.
The cooling water does not come into contact with air and is not exposed to sunlight in a closed cycle, basically eliminating the need to replenish fresh water. The process by-products and dust collected during the production process are also recycled and reused in a uniform manner, effectively achieving zero emission as well as cost reduction and efficiency enhancement.
Developing silicon-based defoamer to improve wastewater treatment efficiency
Foaming from industrial wastewater can reduce water treatment efficiency. Elkem’s innovative silicone defoamer SILCOLAPSETM not only has fast defoaming performance, but also has excellent and long-lasting foam suppression ability. It is like a responsive athlete who can quickly respond to wastewater foam in a short period of time and has a wide range of applications, enabling it to perform excellently in different environments.
Information-based monitoring, lean management
All over the world, Elkem has professionally surveyed and documented the condition of water resources, watersheds, and ecosystems in the vicinity of its plants, and has set sound water management goals. Elkem Xinghuo Silicones has also established an online monitoring platform for energy consumption, improved water metering facilities and linked the data to a real-time database system. It takes information technology to accurately monitor water consumption in all aspects of production and carries out targeted water-saving actions based on reliable data support.
Deeply developing the potential of water-saving in various production links
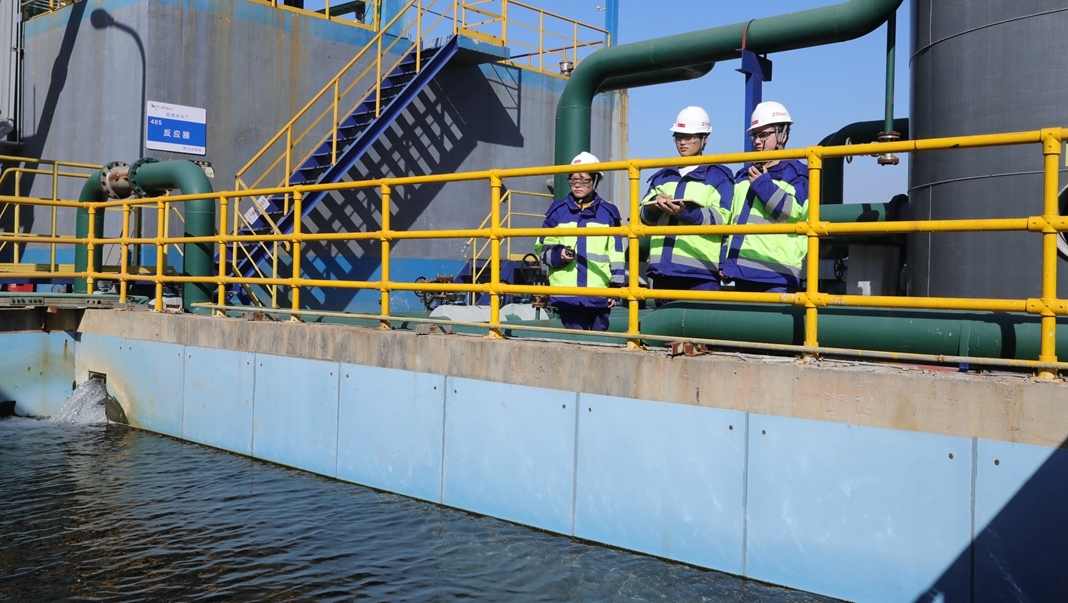
Through a series of water-saving projects such as boiler water treatment technology and condensate steam recovery, circulating water instead of primary water cooling, as well as projects such as upgrading sewage discharge standards and recycling drainage water.
Elkem Xinghuo Silicones has achieved annual water savings of more than 3 million m3. In recent years, the company has been awarded honorary titles such as “Water Saving Benchmark Enterprise” and “Water Efficiency Leader” in Jiujiang City and Jiangxi Province.
Adisseo: Committed to reducing water consumption per ton of product by 20% compared to 2015 by 2025
To reduce the environmental impact of its production activities, Adisseo has invested more than EUR 80 million in this field over the past five years. In terms of improving wastewater treatment plants, significant results have been achieved at plants in China, Spain, and France. Adisseo has set a target of reducing its water consumption intensity (quantity of water used per ton of product manufactured) by 20% by 2025 compared to 2015.
Optimizing water use behavior
To reduce the environmental impact of its production activities, Adisseo has invested more than EUR 80 million in this field over the past five years. In terms of improving wastewater treatment plants, significant results have been achieved at plants in China, Spain, and France. Adisseo has set a target of reducing its water consumption intensity (quantity of water used per ton of product manufactured) by 20% by 2025 compared to 2015.
Taking the Adisseo Nanjing Plant (BANC) as an example, instead of discharging wastewater, a production plant uses wastewater recycling to replace desalted water, reducing the amount of effluent discharged by more than 16,000 t/a and saving RMB 150,000. Following the same principle, a water reuse loop has been created on an ammonia solution preparation plant, thus avoiding the use of more than 3,500 t/a of desalinated water, resulting in an economic benefit of over RMB 60,000.
Investing in the construction of high-standard wastewater treatment plants
Adisseo has built a new Odisseo sewage treatment plant at the Commentry factory in France. Meeting the most stringent regulatory requirements, the treatment plant has reduced COD (chemical oxygen demand) emissions by 40% and TSS (total suspended solids) emissions by over 70%.
Another positive result is that sludge volumes have been reduced by two-thirds and all site quality requirements can be met. Moreover, a project to rehabilitate the old effluent storage tank and sludge storage area has been initiated to ensure that the plant’s production activities are fully harmonized with the environment.
Improving the level of effluent control
At the La Rochelle plant in France, the “Ekeau project” has been launched to optimize the level of control of industrial effluent through the installation of a hydraulic regulation basin and a safety basin. This project also includes the complete renovation of all rainwater collection and treatment facilities as well as several water-saving measures to reduce the number of washing operations and encourage recycling and reuse.
Developing water-saving and alternative products
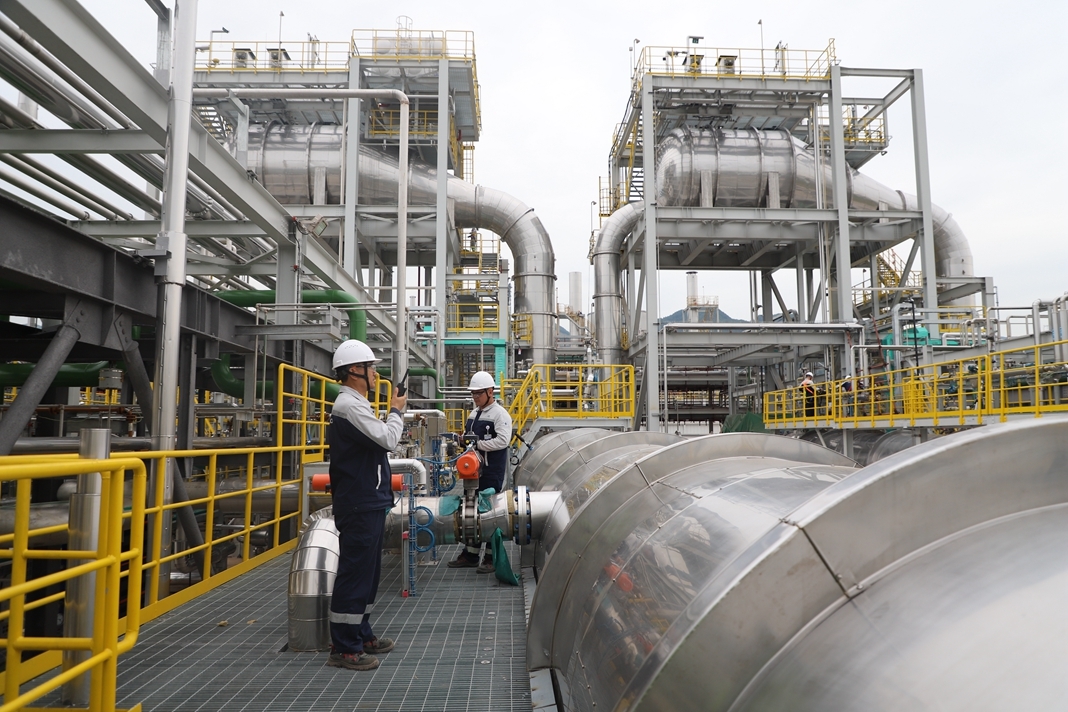
Water is essential for aquaculture. Mainly fermented from natural gas, Adisseo FeedKind® single cell protein is a non-GMO feed ingredient produced without relying on water. Using 100,000 tons of FeedKind® single cell proteins can save 9 billion liters of water.
Little drops of water do represent the most critical issue. Bluestar, focusing on water environmental protection, strives to be a leader in water efficiency in the chemical industry by systematically promoting water control paths and establishing high-level ecological models.