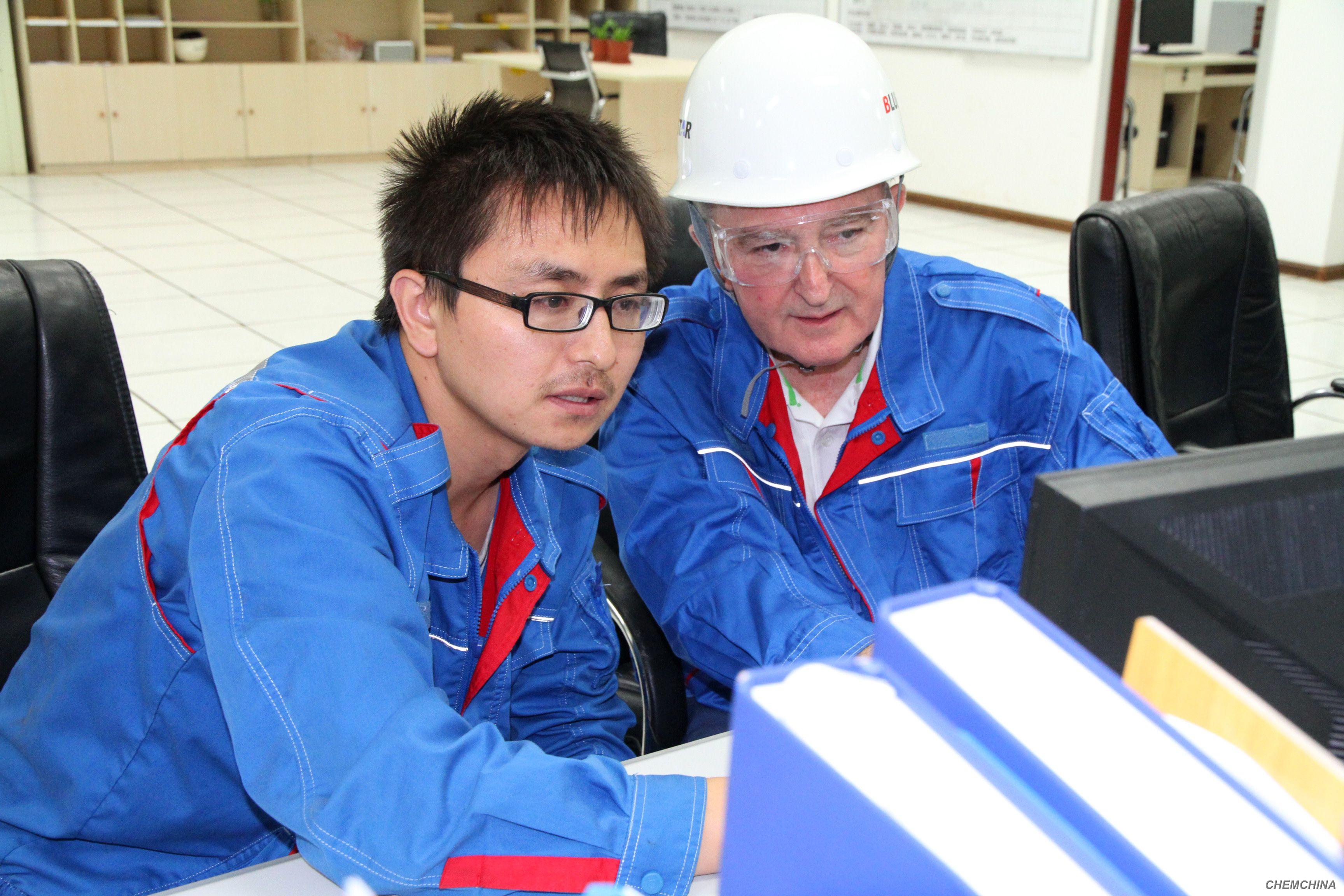
“2016年4月,0.85;5月,0.89;6月,0.90;7月,0.91……”
这是星火有机硅三分厂一页普通的操作记录,我们甚至会忽略这一连串日期和数字里细微的变化。可谁能想到,这每一个0.01的进步,就能为企业节省6万余元。这些数据记录的是每个月天然气加热炉的热效率值,也记录着郑士朋和团队为此付出的心血和汗水。
郑士朋,这位三十出头的工艺工程师是郑州大学化工工艺专业硕士,他爱化工,爱有机硅,以解决工艺难题为乐,容不下任何一个工艺问题。他说,寻找方法的过程虽然有些辛苦,但解决问题的成就感很能鼓舞自己。入厂刚半年时,他这个新员工便尝试将所学知识结合生产实际,大胆提出了降低氯甲烷消耗的设想,经论证应用后大大降低了有机硅分厂氯甲烷生产消耗,深受领导与同事好评。
2010年,郑士朋经分厂推荐,通过厂里的层层考核与法国BSI专家面试,成功应聘为新20万吨有机硅改扩一体化项目法国BSI专家助理。他抓住宝贵的学习机会潜心钻研,有机硅合成、硅粉、循环水、冷冻水系统等岗位,都留下了他和法国专家孜孜不倦探索最佳工艺的身影。BSI专家团队离厂后,积累了丰富实践经验的郑士朋全面接手相关工作,挑起了合成、硅粉与公用工程工艺技术的大梁。在郑士朋的带领下,项目工程进度加快。他先后发布了导热油、硅粉破碎、研磨等系统的最终版安全矩阵并主持测试,编写了破碎、研磨等程序并进行全面离线测试。此外,他还全面参与导热油、硅粉与合成的试车,解决试车过程中出现的问题,总结经验并提出优化操作方案。
此后,郑士朋利用专长,在维护生产平稳运行的前提下,马不停蹄地开展了多个优化项目,综合提高加热炉热效率便是其中一项。导热油系统有多个加热炉,每班用气量巨大,加热炉热效率非常低。郑士朋借来一支红外测温枪,对加热系统、油管网及用户的保温进行了全面测试和统计。他还特意向检验中心请教加热炉尾气中各种气体的测试方法,在学会使用奥式气体分析仪之后,他就像着了魔一样,不分白天黑夜地测试尾气变化情况。经过不懈的努力,郑士朋终于找到影响加热炉热效率的原因,并有理有据地提出了改进方案:通过优化生产导热油管线,充分利用一次用户的余热,提高加热炉进出口油温差,对加热炉负荷进行调整,引入富氧空气,以达到综合提高加热炉热效率的目的。该项目现已成功,每月可为企业节省30余万元。
对于硅粉输送系统的改造则是又一个成功案例。这套系统涉及近50个阀门、20个子程序,由于系统设计与实际应用之间契合度欠佳,系统无法实现自动运行。合成生产运行时,每一个班的操作中,工人要手动动作该部分阀门近2000次,不仅劳动强度大,还易因手动操作缺乏稳定性而造成阀门堵塞。郑士朋结合实际操作提出优化方案并实施,采用输送重量与压力配合等自动判断操作,成功解决自动化瓶颈。硅粉车间硅耗居高不下,不仅浪费原料,还有污染环境的风险。郑士朋提出将几个硅粉仓串联起来共同使用,降低压力与速度,防止硅粉在生产过程中的累积;并通过改造减轻过滤器的负荷,使用特殊材料制品替代管线连接,减少硅粉泄漏,一举解决硅耗难题。
十足的责任心加上过硬的专业素养,郑士朋将民族有机硅之梦作为个人不断前行的动力,立足岗位,努力实践成长,为企业战略推进和可持续发展不断做出贡献。